Automated production of containers, kegs, boilers, pots and pans
Precisely scaled to application area and output
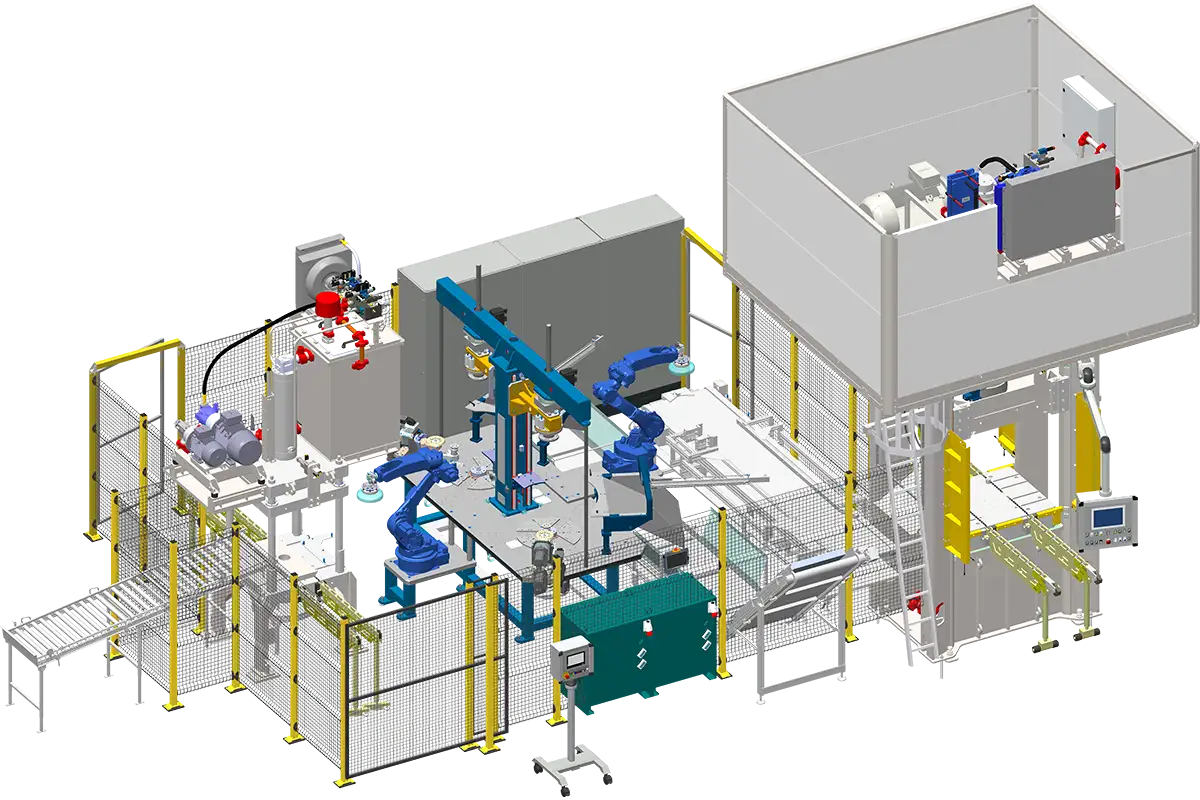
The concept
KURTH + HEUSER develops and manufactures machines for all individual process steps involved in automated high-volume series production of containers as well as entire systems. Proven standard components are coordinated and can be integrated, for example with robotic systems, into high-performance manufacturing systems.
Highlights
- As in-line solution or stand-alone concept
- Automation according to requirements
- Special edge preparation for laser welding
- Economic changeover concepts up to just-in-sequence production
- Combination of standard and custom machines
- Remote diagnostics via LAN, WLAN or GSM
- CE-compliant comprehensive documentation of overall system
Flexible high-precision manufacturing
Production lines from KURTH + HEUSER can be easily converted to different lengths, diameters, shapes and processing methods. To this end, a large number of individual steps such as trimming, forming, punching and joining, assembly, welding and testing are adjusted to the new task automatically and with ultimate precision. The preparation of edges for the welding process is of major importance to ensure the highest level of process reliability and a minimal number of failed parts.
High system availability
KURTH + HEUSER systems are designed for a long service life and ultimate availability: Durable individual components, proven standard components, parts from renowned manufacturers, tools with long service lives as well as a customer service for regular maintenance and adjustments to new requirements.
Processing methods
- Trimming and preparation of edges for welding, e.g. laser welding
- Forming and welding of shells from sheet metal blanks
- Punching, embossing and forming of the shell for filler necks, measuring devices, handles, feet, mounts, edge attachments, etc.
- Trimming and beading of vessel heads
- Joining and welding of vessel heads and shells
- Welding of filler necks, flanges, handles, feet and edge attachments
- Leak testing of finished products
You are currently viewing a placeholder content from Default. To access the actual content, click the button below. Please note that doing so will share data with third-party providers.
More InformationProduction system for edge processing of boiler bottoms
Automated cell for edge processing of boiler bottoms.
Processes:
– Trimming
– Beading
– Rounding the edge
Both machines are loaded and unloaded by a robot.
You are currently viewing a placeholder content from Default. To access the actual content, click the button below. Please note that doing so will share data with third-party providers.
More InformationEdge processing machine KH-650-R-H for vessel heads
KURTH + HEUSER – machines are designed as modular systems. This means they can be flexibly equipped with the right processing units and customised for a wide range of workpiece geometries and tasks.
You are currently viewing a placeholder content from Default. To access the actual content, click the button below. Please note that doing so will share data with third-party providers.
More InformationTrimming and forming machine KH-650-R-E
Edge processing machine for preparing the weld edges of vessel heads (e.g. boilers).
You are currently viewing a placeholder content from Default. To access the actual content, click the button below. Please note that doing so will share data with third-party providers.
More InformationKH-602-R-H Expansion vessels
Fully automatic production cell for the manufacture of expansion vessels, for example. The cell is designed for an output of 3 expansion vessels per minute.